金屬薄壁零件切削過程的三維仿真
2016-12-16 by:CAE仿真在線 來源:互聯網
薄壁零件具有結構緊湊、質量輕的優點,在航空航天、精密儀器等領域應用廣泛。這類零件由于壁薄而導致低剛度、易變形,在切削加工過程中,切削力、裝夾的夾緊力等因素作用都會引起工件變形。加工結束后工件所受外載荷消失,彈性變形恢復,使已加工工件的精度受到嚴重影響。這種情況制約了薄壁零件的加工質量與加工效率的提高。因此研究薄壁零件的切削過程,對控制薄壁零件加工變形、提高加工質量具有重要意義。傳統切削研究主要采用試驗研究與理論結合分析的方法,需要以大量的實驗為基礎,且難以取得關于切削過程參數的精確解析解。隨著虛擬科學與工程的發展,采用計算機數值模擬技術對切削過程進行仿真研究成為重要的研究方法。本文采用Deform3D有限元軟件對45鋼材料薄壁零件的切削過程進行仿真實驗研究,精確取得了切削力、應力場、溫度場及切削變形等切削過程參數預測值。
1 切削過程有限元建模
金屬切削過程屬于大變形的幾何非線性問題,工件切削層材料在前刀面推擠作用下發生塑性流動。切削層材料在切削過程中發生連續動態的大變形,使初始網格畸變,導致求解困難甚至無法繼續計算。Deform軟件采用經過特殊處理的四面體單元,并具有自適應網格劃分技術,可在切削過程中即時動態地自動重新劃分網格。為定義工件材料在切削力作用下的響應,需要建立其材料模型,Deform提供了豐富材料庫,可直接提取所需材料模型。切削過程中切削層不斷從工件基體材料上分離形成切屑,切屑分離準則應能準確反映切削層分離的實際過程。Deform默認的缺省準則是當接觸節點的拉應力或壓應力大于0.1MPa時,節點分離。切屑形成后沿前刀面流走,因此切屑底面與前刀面間產生摩擦,在靠近刀尖處的粘結區(Stick),刀—屑間的摩擦是材料內部的滑移剪切,摩擦力等于剪切流動應力;而較遠的滑移區(Slip)摩擦為外摩擦,摩擦力服從庫倫摩擦定律。刀具切入工件,兩者發生接觸,可看做是剛體—柔體的接觸,其中,刀具材料硬度較高,定義為剛體;工件硬度低,則定義為柔體。劃分單元時,柔體應有較剛體更加細密的網格。當刀具與工件上的節點相互接觸時,接觸節點保持在剛體表面運動,因此兩者不會互相穿透,直到分離。若柔體上節點受力為壓應力狀態,則認為與剛體的表面接觸;若該節點所受拉應力大于給定值,則認為節點脫離接觸體表面。Deform-3D采用可靠的主從算法,在接觸搜索過程中不允許柔體上的節點穿透剛體表面,只需在柔體節點與剛體表面間進行接觸搜索,計算效率得到提高。切削過程中,刀具發生磨損,為使研究更加接近實際,應建立刀具磨損模型。在Deform中,常用Usui粘接磨損特征公式來表示切削過程中刀具的磨損。
2 薄壁零件切削過程仿真
(1)切削模型的建立
刀具模型
從Deform刀具庫中選擇已有的刀具模型DNMA432,刀具材料則由材料庫中提取WC硬質合金。因刀具強度、硬度遠高于工件材料,在切削過程中所產生的應變很小,所以假定為剛性材料,而僅考慮其摩擦、傳熱等效應。為節約計算成本和保證計算精度,設定刀具網格數25000,采用局部動態加密技術對刀尖處局部加密,尺寸比例1:4。刀具模型如圖1所示。

圖1 刀具有限元模型
工件模型
為簡化計算過程,選定薄壁零件中較簡單的薄板形工件為切削研究對象(見圖2),利用Deform平臺的工件形狀設定功能生成零件。為保證計算結果更加接近真實狀況,工件材料選擇彈塑性材料,由Deform軟件材料庫中提取AISI1045,即45鋼材料。劃分工件網格數40000,切削層及附近局部處動態加密,尺寸比例1:7。工件劃分網格后模型見圖3。
切削參數設定
由于高速切削在薄壁零件的加工中有明顯優勢,所以模擬選定切削速度200m/min,進給量0.15mm/r,切削深度0.2mm。選擇Deform系統默認的剪切摩擦模型,摩擦系數設為定值0.6。假定環境溫度為20℃。采用Usui模型計算刀具磨損,系數a=1e-05,b=1000。切削有限元模型見圖4。
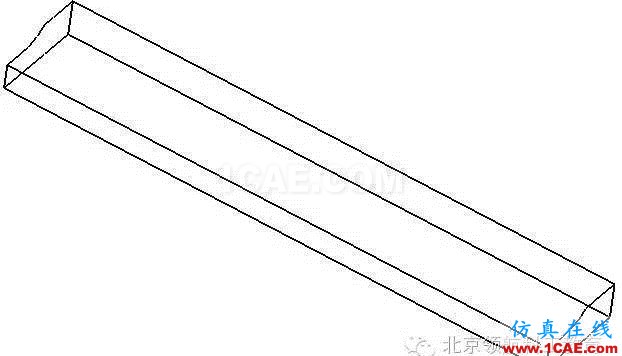
圖2 工件幾何模型
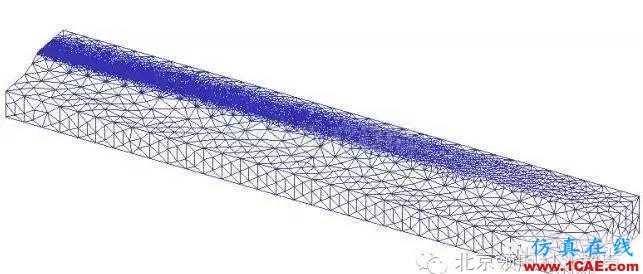
圖3 工件有限元模型
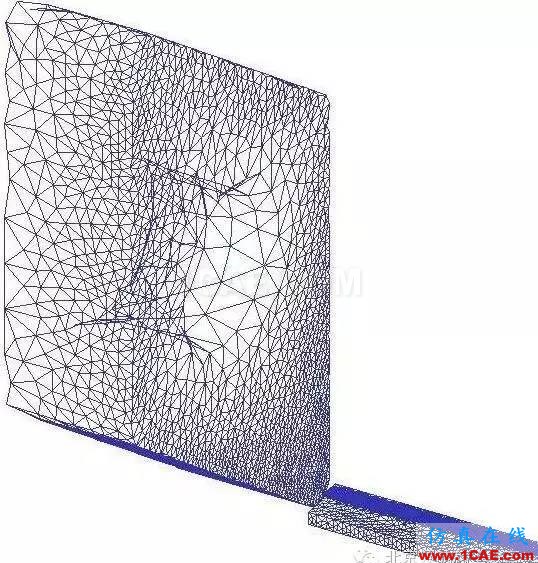
圖4 薄壁件切削有限元模型
(2)仿真結果分析
切屑的形成
切屑的形成過程如圖5所示。刀具切入工件,切削層材料在刀具的推擠作用下與工件基體材料分離,形成切屑,隨著切削過程的持續進行,切屑發生了彎曲變形。
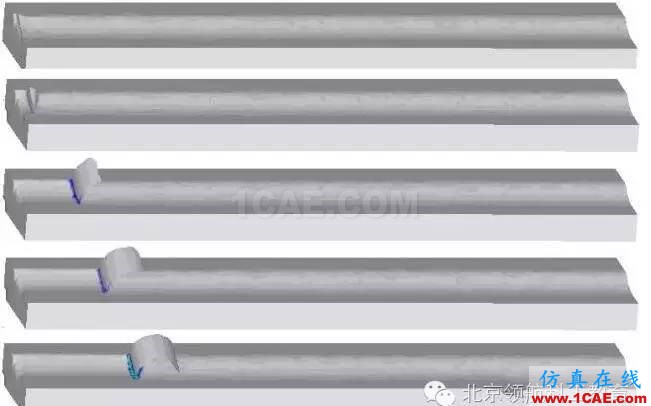
圖5 切屑的形成過程
切削力分析
切削力指切削過程中作用在刀具與工件上的力。作用在刀具上的切削力包括兩方面:工件變形所產生的彈性變形抗力、塑性變形抗力;切削底面與刀具前刀面、工件已加工面與刀具副后刀面間的摩擦力。為便于研究,通常將切削力分解為主切削力、進給力和切深抗力。圖6、圖7、圖8分別為三個方向切削力隨切削進程的變化曲線圖。切削力變化曲線表明,隨著刀具切入工件,三個方向的切削分力變化趨勢大致相同:在接觸開始的短時間內,切削力從0開始迅速增大,隨后進入穩定切削狀態,切屑產生過程平穩,切削力數值也在某一數值附近震蕩。三個力中主切削力最大,是計算機床電機功率、校核機床主要部件強度、設計夾具的重要依據,對切削變形有顯著影響。
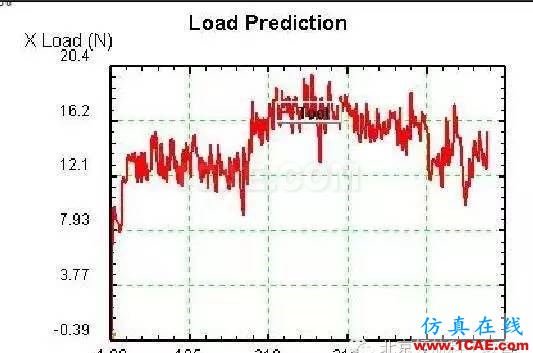
圖6 進給力變化曲線
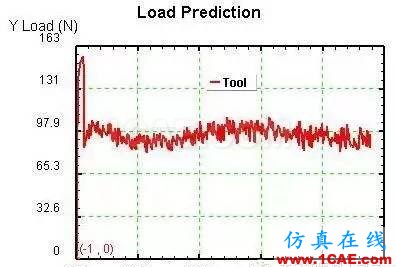
圖7 主切削力變化曲線
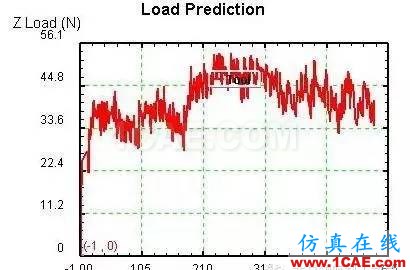
圖8 切深抗力變化曲線
切削應力分析
圖9為工件切削區域等效應力分布圖。由圖可見,切削過程中工件的最大等效應力位于第一變形區和刀尖接觸處。圖10為切削區最大主應力分布圖。可見,工件及切屑中的最大主應力在靠近刀尖處為壓應力,在稍遠處則過渡為拉應力,模擬結果與經典切削理論相符。

圖9 切削區等效應力
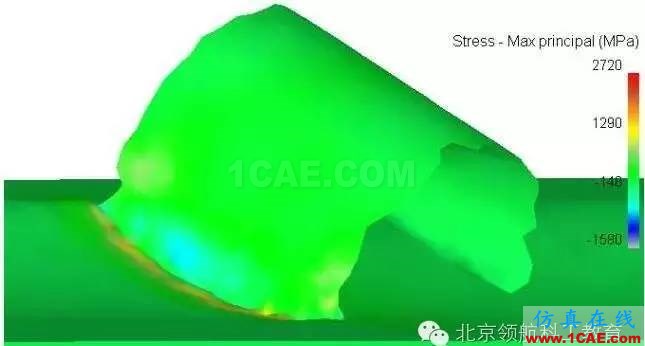
圖10 切削區最大主應力
應變分析
在切削過程中,切削層金屬受刀具擠壓作用,使近切削刃處產生彈性變形和塑性變形并形成切屑。切削刃作用部位的金屬可劃分為三個變形區:近切削刃處切削層內產生塑性變形區;與前刀面接觸的切屑底層產生的變形區;近切削刃處已加工面表層產生的變形區。從圖11及圖12可見,當切削層材料剛從工件基體材料上分離時,等效應變和最大主應變值達到最大。
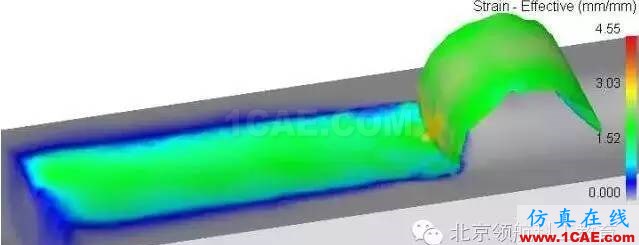
圖11 切削區等效應變
切削溫度分析
切削過程中,切削區域劇烈塑性變形所形成的熱、切屑與前刀面摩擦功形成的熱、已加工表面與副后刀面摩擦形成的熱傳入工件和刀具,使其溫度升高,造成工件變形,加速刀具磨損。由圖13可見,切削熱主要集中在切屑變形處,切削區域溫度最高可達553℃,原因在于該點處受到剪切區變形熱和刀—屑連續摩擦熱影響,熱量集中而又不易傳散。隨著切削的持續進行,已加工面上的溫度迅速降低,所以已加工表面上的溫度相對較低。
圖12 切削區最大主應變
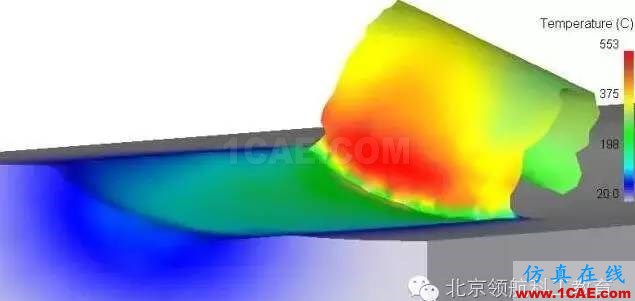
圖13 切削區溫度場分布圖
小結
通過金屬薄壁零件切削過程的三維有限元仿真研究,觀察了切屑的形成過程,并獲得切削力變化曲線、切削應力應變分布圖和切削溫度場分布圖,仿真結果與經典切削理論相符,說明模擬結果正確。仿真結果使實際加工前即可獲取較為精確的切削過程參數的預測值,對優化切削參數、提高加工質量具有重要意義。
文章來源《工具技術》作者:李智
相關標簽搜索:金屬薄壁零件切削過程的三維仿真 Deform有限元分析培訓 Deform學習教程 Deform培訓課程 Deform資料下載 deform視頻教程 Deform代做 deform基礎知識 Fluent、CFX流體分析 HFSS電磁分析 Ansys培訓 Abaqus培訓 Autoform培訓